Three Reasons You Should Add a Torque Wrench to Your Toolbox
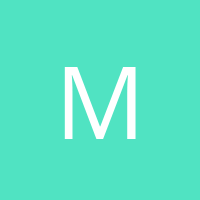
A torque wrench is a valuable tool for anyone serious about their mechanical work. Professional mechanics understand the importance of properly torqued fasteners, which is why they keep a selection of ¼”, ⅜”, and ½” drive torque wrenches in their toolboxes.
Many DIY enthusiasts acknowledge the importance of properly torquing items like lug nuts, cylinder head bolts, and suspension hardware. However, they often overlook smaller components like spark plugs, brake bleeder screws, and hose clamps, deeming them unworthy of the effort. The common misconception is that "tight is tight," but the reality is different.
The spectrum of torque requirements is wide, necessitating the use of multiple torque wrenches for different tasks. Some larger ¾” and 1” drive torque wrenches are rated for more than 500-ft.lbs, which can be useful for single-lug racecars and big rigs. On the other hand, smaller precision ¼” torque wrenches may only operate up to 200-in.lbs (equivalent to 17-ft.lbs), making them great for fine assembly work but not very useful for suspension or larger components.
Whether you're looking to save money by swapping your winter tires at home, building an engine in your living room, or restoring an old car in your garage, a torque wrench allows you to tighten nuts and bolts to a specific level of torque, ensuring that they are neither under-tightened nor over-tightened.
A good torque wrench provides feedback when you’ve applied the specified amount of torque. A click-type torque wrench has a spring-loaded lever that is adjusted by twisting the handle to the desired value. When the proper force is applied, the lever breaks, creating the clicking sound. Electronic torque wrenches use a strain gauge attached to a torsion rod, and the transducer signal is converted to the required unit of torque and relayed via a digital display along with a beep, vibration, and lights, depending on the model. Beam-type torque wrenches measure the deflection of a stressed beam and relay that information to the user on a simple-to-use gauge. Beam types are the most accurate over time but can be challenging to read unless you’re right on top of the gauge.
Regardless of the style you choose, here are three reasons you should consider adding a torque wrench to your toolbox.
1. Prevention of Over-Tightening
The number one killer of fasteners is over-tightening. While tight is certainly better than loose, over-tightening a nut or bolt can lead to damage and distortion of the threads or shank, which are the weakest areas of a fastener.
When a fastener is over-torqued, it can exceed its yield strength and result in the stretching of the threads or, worse, the shearing of the bolt. This can lead to a loss of clamping force and structural integrity. Over-torqued fasteners also undergo increased stress, leading to premature fatigue failure.
This can result not only in cracking or fracturing of the fastener but also in compromising the bearing area of the material or component being fastened. Damaging the bearing area of the material or component can also result in a loss of fastener pre-load, ultimately leading to the paradoxical outcome of an overtightened bolt coming loose. Torque wrenches help prevent these issues by enabling controlled and precise application of torque.
2. Consistency
In applications where multiple fasteners need to be tightened to the same level in sequence, torque wrenches ensure consistency and uniformity across all fasteners. Consider a cylinder head or crank main bearing caps; the fasteners don’t care if they’re tightened in a dorm room or a machine shop–but they do require consistency in application.
When performing engine or suspension work, you will often come across torque to yield bolts that require special sequencing. Initially, they will need to be tightened to a snug value before you are instructed to rotate the fastener to a specific angle.
This process stretches the threads beyond the state of elasticity, bringing the fastener into plastic deformation, and causing it to become permanently elongated. This is detrimental for normal fasteners like wheel studs, but highly desirable in high-frequency, high-stress applications.
Consistency in sequencing is essential for eliminating distortion. Measuring rotation in degrees instead of an applied torque figure ensures that friction does not interfere with an even clamp load. While it is possible to do this with a paint pen and your eyeballs, if you are after consistency and longevity, consider getting yourself a modern digital torque wrench that allows you to specify angle torque. You can also consider a torque angle gauge as an accessory to an existing torque wrench.
3. Cost Saving
In this economy, almost everyone is looking for ways to save a few bucks. One of the best ways to save money is by performing routine maintenance on your car at home. Tasks like seasonal tire swaps, oil changes, and even brake jobs are achievable for almost anyone willing to wield a wrench.
A ½” drive torque wrench, a jack and jack stands, practically pay for themselves after just one year of swapping your wheels each spring and fall. This cost savings scale if your household has multiple vehicles. Without a torque wrench, it is possible to over-torque your wheel nuts and stretch the threads, or worse, leave them loose.
Once you're confident enough with wheel swaps, consider changing your oil, where a torque wrench is useful for tightening the drain plug without over-tightening and risking cracking or deforming the oil pan.
Highest on the routine maintenance complexity scale is a brake job. Regardless of the type of caliper and how it’s secured to the wheel upright, a torque wrench is critical for finishing the job.
Fixed calipers are typically secured with just two bolts or nuts, with torque values often ranging from 50 ft. lbs to more than 100 ft. lbs in some cases. On the other hand, floating calipers use a pair of bolts to secure the anchor bracket to the upright and a pair of slide pins to secure the caliper to the bracket.
Editor's Pick: CDI 1/2-Inch Drive 30-250 Pound Adjustable Micrometer Torque Wrench
Owned by Snap-On, CDI is one of the top names in the torque instrument business. If you’re looking for a high-quality torque wrench that will last a long time, CDI is the choice to make.
The CDI 1/2-Inch Drive 30-250 Pound Adjustable Micrometer Torque Wrench is the same one I have in my toolbox. While the CDI’s 32-tooth head doesn’t provide as tight of a swing arc as the 72-tooth Snap-On torque wrench, the larger teeth are stronger and more durable.
The click-type CDI ½” drive torque wrench is calibrated to ±3% clockwise and ± 4% counterclockwise of the indicated value. If you’re going to get just one torque wrench, this is the one to have. It’s a quality tool capable of DIY or professional work alike.
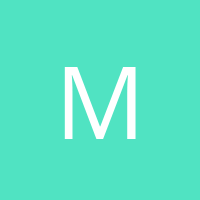
More by Michael Accardi
Comments
Join the conversation
A decent clicker Torque Wrench is gonna run at least 100 bux no matter what drive you get. You'll be buying nothing but frustration if you pay under that!